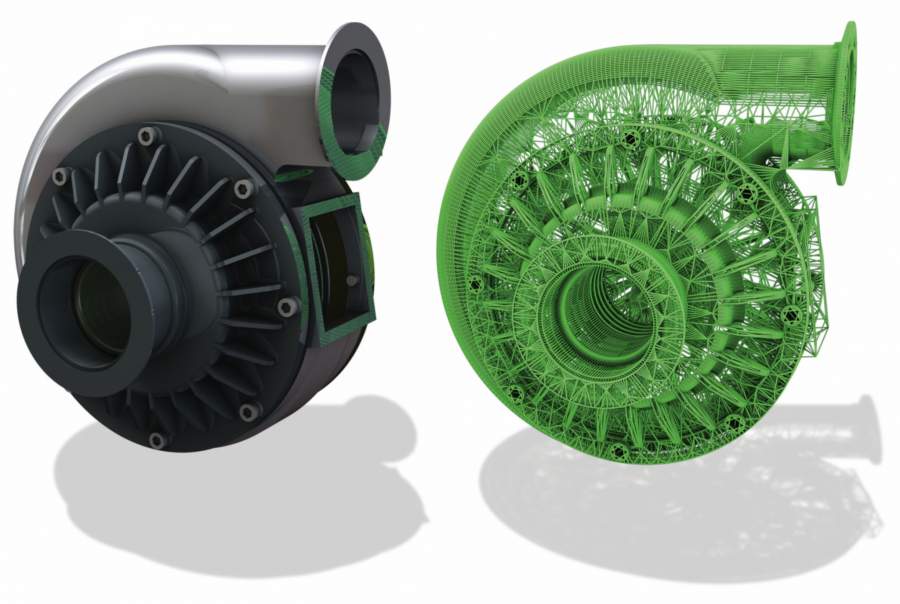
Digitale Zwillinge machen den Lebenszyklus physikalischer Produkte transparent
Digitale Doppelgänger
Digital Twins schlagen eine Brücke zwischen der realen und der virtuellen Welt. Unternehmen aus verschiedensten Branchen machen sich die Technologie zunutze, um Kosten zu senken, effizienter zu arbeiten und ihre Produkte und Dienste zu optimieren.
Ob Motor, Pumpe, Triebwerk, Fahrstuhl, Windrad oder Smart Home: So ziemlich alle in der realen Welt existierenden Maschinen und Geräte lassen sich in Software abbilden. Auch kleineren oder größeren Infrastrukturen kann man einen virtuellen Zwilling an die Seite stellen. Das gilt für Fabriken, Kraftwerke, Bohrinseln und Rechenzentren genauso wie für Telekommunikationsnetze oder für die Verkehrssteuerung und das Abfallmanagement von Gemeinden („Smart City“).
Digital Twins sind ein nächster Schritt in der Evolution von Produktionsprozessen, die mit CAD- und Simulationssoftware, mit 3D-Modellen sowie SCADA- und PLM-Tools in das digitale Zeitalter eintraten. Es sind in der Cloud beheimatete digitale Abbilder physikalischer Produkte, Prozesse oder Dienste (zusammenfassend: Assets), die mit diesen dauerhaft im Netzwerk verbunden sind. In der Regel existieren sie während der gesamten Lebenszeit des Vorbilds und durchlaufen die gleichen Entwicklungsphasen – von der Konzeption bis zur Ausrangierung.
Möglich wird das digitale Abbild erst durch das Dreigespann IoT, Big Data und maschinelles Lernen. Im Industrial Internet of Things (IIoT) lässt sich nahezu jedes Betriebsmittel mit Sensoren versehen. Die Verarbeitung dieser Sensordaten kann in vielen Fällen bereits „at the Edge“, in der Nähe des physikalischen Objekts, erfolgen. Das bringt Geschwindigkeitsvorteile, spart Bandbreite und verringert die Anforderungen an die Speicherkapazität in der Cloud. Die gesammelten Daten fließen in einen Data Lake, wo Analyse-Tools aus dem Big-Data-Bereich und selbstlernende Algorithmen sie auswerten und mit Informationen aus anderen Quellen verknüpfen. Sie finden Zusammenhänge, Trends, Muster und Auffälligkeiten. Künstliche Intelligenz („Deep Learning“) spielt in diesem Rahmen auch eine immer wichtigere Rolle.
Bei der Modellierung eines digitalen Zwillings werden die relevanten Kennzahlen und Parameter definiert und (außer beim Prototyping) mit den Werten des realen Geschwisters in seiner konkreten oder beabsichtigten Umgebung gefüllt. Angereichert werden die Messdaten – wie Status, Druck, Temperatur, Batteriezustand oder Geschwindigkeit – mit Metadaten aus zusätzlichen Quellen. Das können zum Beispiel aktuelle Wetterdaten sein, aber auch Infos aus der Wartungshistorie baugleicher Geräte oder des Vorgängerprodukts. So entsteht ein Abbild, das mehr ist als die bloße Summe der gesammelten Sensordaten.
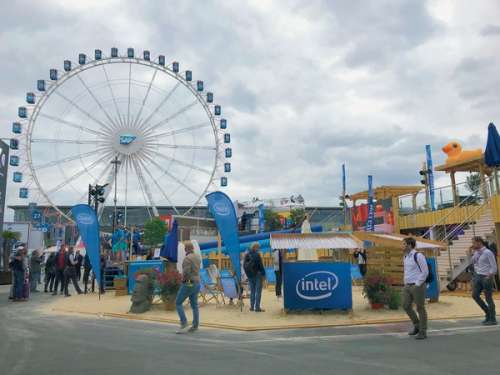
Zweirichtungsverkehr in der digitalen Nabelschnur
Der virtuelle Wegbegleiter gibt seinen Schöpfern jederzeit Einblick in den Zustand seines Geschwisters in freier Wildbahn. Darüber hinaus bietet er sogar einen Blick in die Zukunft, indem er mithilfe von Simulationen und Predictive Analytics vorhersagt, wie sich das Original perspektivisch oder bei geänderten Parametern verhalten wird. Die virtuelle Nabelschnur muss indes keineswegs eine Einbahnstraße sein. Neben Sensoren können Assets auch Aktuatoren enthalten. Sie erlauben im gewissen Rahmen eine Steuerung aus der Entfernung, wenn Ist- und Sollzustand nicht miteinander im Einklang sind. Besonders praktisch ist dies in Situationen, in denen das physikalische Asset nur mit großem Aufwand erreichbar ist oder sich in einer Gegend befindet, die für Menschen gefährlich ist.
Je nach Branche, Anwendungsfall und Unternehmensziel variieren die digitalen Doppelgänger enorm in Komplexität und Granularität. Zu einem Asset können auch mehrere Abbilder existieren, mit unterschiedlichen Konfigurationen für unterschiedliche Szenarien oder Teilbereiche. Oft wird es einen sogenannten Digital Master geben, von dem Abbilder für die konkreten Assets (zum Beispiel einzelne Windräder) abgeleitet werden.
Umgekehrt ist es möglich – und oft empfehlenswert, denn sonst droht „Overengineering“ –, nur die wichtigste(n) Komponente(n) eines Systems in Software zu modellieren. Für eine Klimaanlage wäre das zum Beispiel der Kompressor.
Anforderungen an eine Digital-Twin-Plattform
In vielen Fällen werden digitale Zwillinge auf Basis von IoT-Plattformen entwickelt. Bei der Auswahl einer geeigneten Technologie spielen viele Überlegungen eine Rolle. Wie flexibel ist die Software und wie zuverlässig? Wie gut skaliert das System und wie lässt es sich verwalten? Aber auch: Wie kann es an bestehende Systeme angebunden werden und wie funktioniert die Absicherung gegen Angriffe oder unbefugten Zugriff?
Eine Digital-Twin-Plattform sollte eine Art von Product-Lifecycle-Management bieten. Damit lässt sich der digitale Zwilling entwerfen, entwickeln, testen, einsetzen und verwalten. Änderungen am konkreten Asset müssen in sein digitales Abbild zurückfließen, damit beide Systeme jederzeit kongruent sind. Die Plattform benötigt offene Schnittstellen, über die der Twin mit anderen Anwendungen wie SCM- oder ERP-Systemen kommunizieren kann. Über eine Anbindung an das unternehmensinterne Rechtemanagement sollte die IT-Abteilung den nutzer- oder rollenbasierten Zugriff auf den Digital Twin steuern können. Ein integriertes Prozessmanagement erlaubt es, bei Erreichung bestimmter Schwellenwerte automatisch bestimmte Events oder Geschäftsprozesse auszulösen.