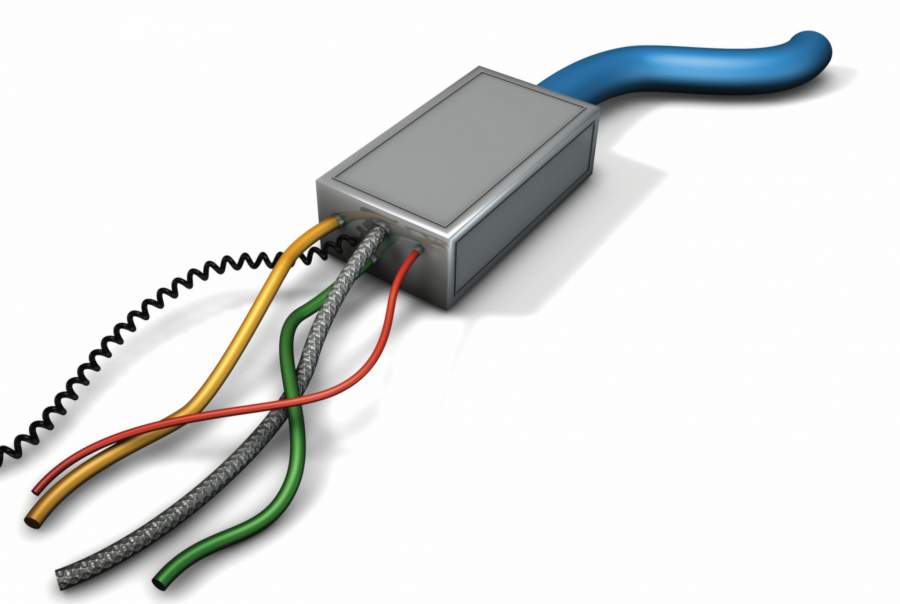
Generische Schnittstelle für Produktionssysteme
API-Salat
Verschiedene IT-Systeme zu koppeln, ist umständlich und kostspielig. Eine standardisierte Schnittstelle würde vieles erleichtern.
Die zahlreichen IT-Systeme in Unternehmen kommunizieren in der Regel über Schnittstellen, deren Entwicklung aufwendig und teuer ist. Hauptsächlich geht es dabei um den Abgleich unterschiedlicher Datenformate. Tendenziell fördert diese Situation den Einsatz monolithischer Systeme und steht damit moderneren Ideen wie serviceorientierten Architekturen (SOA) und Microservices im Weg.
Zwar decken die eingesetzten ERP-Anwendungen schon viele Bereiche ab und arbeiten unabhängig von der Branche. Spezialfunktionen fehlen jedoch oft. Unternehmen sind daher häufig gezwungen, zusätzliche Produkte einzusetzen. Dazu gehören:
– Das Advanced Planning System (APS) oder Leitstand. Es plant die Termine der Fertigungsaufträge bei begrenzter Kapazität.
– Warehousemanagement-Systeme (WMS) steuern häufig in Kombination mit einem Transport Management System (TMS) den innerbetrieblichen Transport und die Lagerhaltung.
– Die Betriebsdatenerfassung (BDE) registriert den Start und das Ende der Bearbeitung eines Auftrages sowie dessen Mengen und Zeitverbräuche.
– Distributed-Numerical-Control-Systeme (DNC) verteilen CNC-Programme (Computer Numerical Control) an die benötigten Maschinen und verwalten gegebenenfalls mehrere Versionen dieser Anwendungen.
– Prüfpläne und Messergebnisse werden von Computer-aided-Quality-Systemen (CAQ) verwaltet.
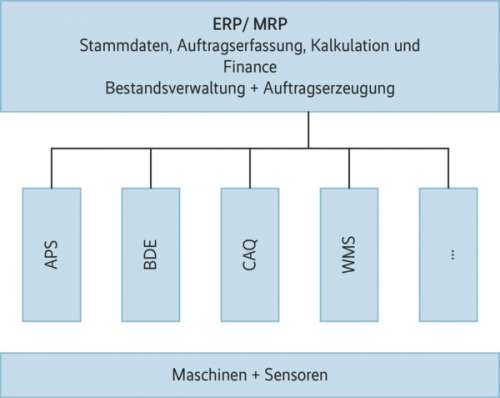
Häufig werden die von den geschilderten Anwendungen bereitgestellten Aufgaben und Funktionen in einem Manufacturing Execution System (MES) gebündelt und als integrierte Lösung angeboten. Koppeln muss man die verschiedenen Komponenten mittels individueller Programmierung selbst. Und das ist wie gesagt suboptimal und verlangt nach einer generischen Schnittstelle.
Abstimmungen deutlich verringern
Dieser Artikel zeigt, wie eine standardisierte Übergabe von Daten beschaffen sein könnte. Dazu müssen zunächst die zu übertragenden Inhalte festgelegt werden. Danach geht es um Techniken zur Umsetzung. Ziel ist, den Abstimmungsaufwand zwischen Softwareanbietern und Kunden deutlich zu reduzieren. DIN oder ähnliche Organisationen könnten die Schnittstelle später normieren und so die Anwender in die Lage versetzen, ihre Systeme weitgehend via Plug-and-Play zu koppeln.
Bis auf das Warehousemanagement-System und den Leitstand betrachten alle genannten Anwendungen lediglich die Fertigungsarbeitsgänge. Deshalb geht es zunächst um den Austausch derselben. Sie sollten mindestens enthalten: Auftragsnummer, Materialnummer und -beschreibung, Arbeitsplatz, Rüstzeit, Bearbeitungszeit und Plantermine. Die Betriebsdatenerfassung ergänzt diese Datensätze um einen Vorgangsstatus (Bereit, Angefangen, Fertig) sowie Rückmeldemengen und -zeiten. Anforderungsabhängig können die Anwender die Bearbeitungszeiten noch in Maschinen- und Personalzeiten sowie gegebenenfalls Energieverbräuche unterteilen.
Das wäre der Minimalstandard. Viele BDE-Systeme erfassen zusätzlich Gemeinkosten ohne Auftragsbezug und Störungen. Meist werden sie über Dummy-Aufträge abgebildet, weitere Anpassungen sind also nicht notwendig.
Distributed-Numerical-Control- und Computer-aided-Quality-Systeme stellen zusätzliche Datensätze pro Arbeitsgang zur Verfügung. Bei DNC handelt es sich um CNC-Dateien, bei CAQ um Prüflisten. CAQ erfasst darüber hinaus Messergebnisse zu jedem Teil in einem Vorgang. Dazu werden zu jedem Arbeitsgang entsprechende Informationen hinterlegt. In aller Regel müssen die Anwender Prüfpläne, Programme und Werkzeuglisten erstmalig bei der Konstruktion eines Bauteils festlegen. Die Daten beziehen sich daher auf einen Arbeitsgang im Stammplan.